Local Storage seems to be disabled in your browser.
For the best experience on our site, be sure to turn on Local Storage in your browser.
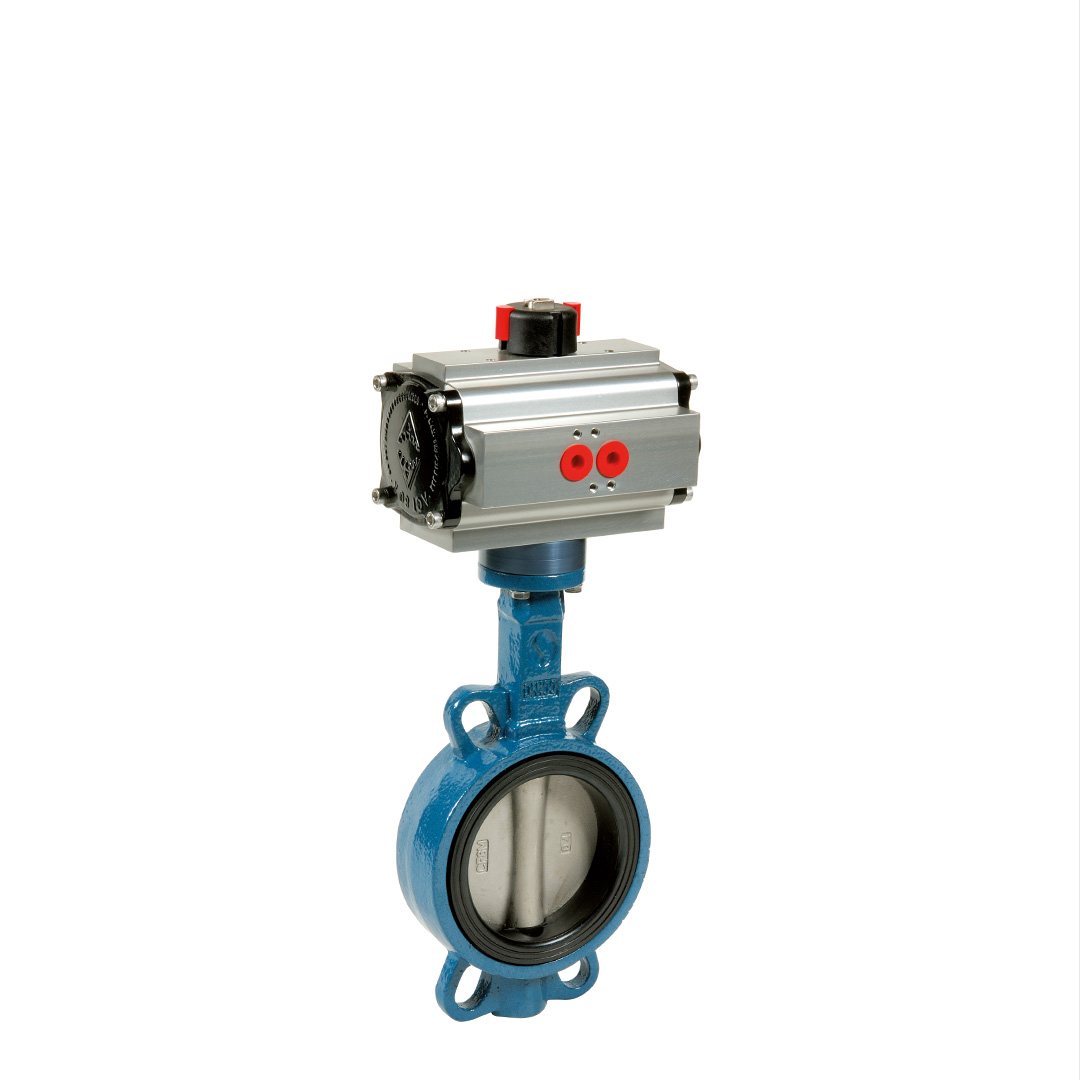
Pneumatic actuation
Purpose
Pneumatic actuated valves represent a very large range of devices. This presentation only introduces the most common of them: ball valves and butterfly valves fitted with pneumatic actuators. Both these types of valves are perfect and cost-effective with a system of pneumatic drive. These actuated valves role is to cut off fluid conducts and tanks thanks to a remote pneumatic control. These valves are most often used for pipe sectioning, machine feeding, by-passes, distribution, venting systems, facility draining, fluid mixing and distributing.
Pneumatic actuated valves are “on/off” fitting devices, which means they are either opened or closed, and they can move from one position to the other instantly. If the valve is to be used for regulation, a specific control valve will be the right choice.
Fields of application
Pneumatic actuated valves are used in every branch of the industry dealing with compressed air systems: valves for water treatment, valves for process networks, valves for steam systems, valves for compressed air, valves for heat transfer fluid, hot water, cold water, glycoled water (reheating, cooling, exchanger). Valves for fire systems, gas systems, fuel systems (oil). They are found in multiple areas such as energy, mining, chemicals, petrochemicals, water treatment, paper mills, laundry, agri-food industry, cosmetics, pharmacy, etc.
Pneumatic actuated valve operation
Double-acting pneumatic actuated valve: a rack and pinion actuator drives the quarter-turn valve stem. A distributor alternatively sends a pneumatic signal through one chamber or the other, allowing the valve to open or close.
Spring-return pneumatic actuated valve: the air cylinder is fitted with springs in order to push the piston back. The pneumatic signal only drives one movement (opening or closing), and the springs operate the other movement. This system allows a safety position in case of a power cut.
Brands
We offer a wide range of pneumatic actuated ball valves and butterfly valves, with actuators coming from different brands: Nutork (NKD/NKS series), Actreg (ADA/ASR series), Alphair (RE/RES series) and El-o-matic (PD/PE series).
Certifications
Depending on the models, our valves have the following certifications: CE PED 2014/68/EU, ISO 9001, ACS, ATEX, FIRE SAFE, TA-LUFT, ISO 5211.
Our pneumatic actuators also have these certifications, and comply with the following standards (depending on the references): CE, ISO 9001, ATEX, SIL, IP, NAMUR VDI/VDE 3845, ISO 5211 and DIN 3337.
Usage restrictions
Although they are very useful in multiple sectors and applications, pneumatic actuated valves can be unadapted to a number of situations:
- No compressed air: in that case, a valve driven by an electric actuator will be a better choice.
- If compressed air pressure is too low: normal operation requires a 6-bar air pressure. A lower pressure can cause malfunctions, and the valve will not work under 5 bar.
- If the fluid is too much loaded: ball valves and butterfly valves are not adapted for use with loaded fluids. The solution is a pneumatic actuated knife gate valve.
- Operating conditions: our pneumatic actuated valves are adapted for use with non-corrosive fluids from -40 °C up to +250 °C, and from 0,5 up to 100 bar depending on the valve models.
Pneumatic actuated valves options
Various and numerous options are available with pneumatic actuated valves:
- Solenoid pilot valve: directly mounted on the actuator and complying with the NAMUR standard, this device is used to control the actuator compressed air supply.
- Throttle valve: mounted on the actuator exhaust, it allows a longer operating time if needed.
- Positioner: used to turn an on/off valve into a control valve. This option is not compatible with every fluid.
- Declutchable gear box: to declutch the pneumatic actuator and manually operate the valve with the gear box.
- Limit switch box: fitted on the actuator, used to communicate the valve position to the control system.
- Stem extension: it is used when the valve is lagged, or to isolate the actuator from a fluid high temperature that could damage it.